450 millimetri di titanio per fermarsi a velocità ultrasonica…
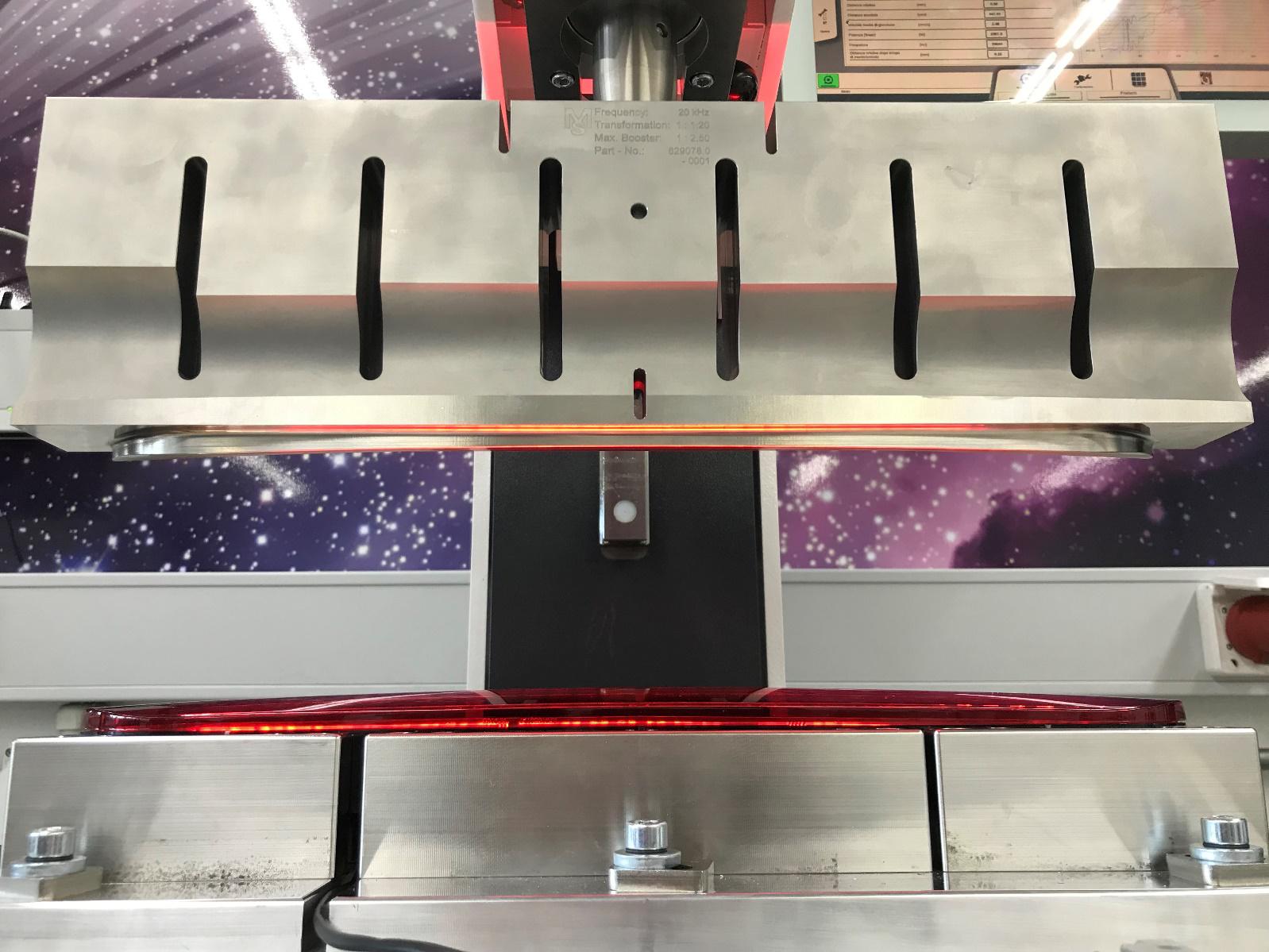
“La situazione è disastrosa. 70% di scarti nelle giornate buone. Perdite, segni estetici e bave degne di un’eruzione dell’Etna…però sai, Ferrari è un cliente prestigioso e va mantenuto a qualsiasi costo, anche rimettendoci pesantemente su ogni pezzo venduto”.
Così Davide, responsabile dell’ingegneria di processo in una delle storiche aziende automotive del modenese, mi aveva descritto l’attuale produzione del terzo stop per le vetture di Maranello.
Quello che era iniziata come un’avventura per un cliente illustre si era trasformata rapidamente in un incubo per tutti i ragazzi della produzione (e dell’amministrazione……).
“Con questo nuovo terzo stop non possiamo sbagliare. Ne va della mia reputazione all’interno dell’azienda come per quella dei miei ragazzi”. Davide era estremamente determinato dopo l’ultima profonda bruciatura dell’attuale fanale.
L’obbiettivo per me era chiaro:
-
Tenuta ermetica a 1,5 bar
-
Saldatura profonda e costante su tutta la lunghezza del direttore di energia
-
Estetica maniacale (il minimo segno estetico non sarebbe stato accettato)
I volumi erano chiaramente molto contenuti come ci si aspetta da un’auto supersportiva di lusso che costa oltre 400.000 €: minimo 2.500 pezzi all’anno fino a un massimo di 5.240.
La Ferrari non è per tutti e questo va chiarito fin dal più insignificante dei dettagli!
La fase progettuale è durata diversi mesi.
Modifica di alcuni dettagli, dimensioni esterne e della regione di giunzione.
I materiali sono i classici ABS+PC per il corpo e PMMA per la lente.
La lente misura oltre i 400 mm con una forma ondeggiata di tipo 3D asimmetrico, quasi un baffo allungato con due appendici finali. La regione di giunzione e il direttore di energia devono chiaramente permettere una fusione precisa, robusta e a tenuta ermetica. In realtà la parte più complessa è che il direttore di energia deve anche permettere la compensazione della possibile (cioè sicura!) non planarità e i il ritiro che sicuramente sarà di almeno 2 o 3 decimi.
Magari a te potrà sembrare poco, ma nella saldatura a ultrasuoni in cui è di fondamentale importanza rispettare il singolo micron nella vibrazione e il centesimo nella profondità di fusione relativa i decimi di millimetro sono come i secondi per i ciclisti o i grammi di peso corporeo per i pugili.
Il tipo di giunzione scelta è stata la STEP sia per semplicità di stampaggio che per il fatto di non poter modificare il design a cui è abituato il cliente. Per il PMMA l’angolo di innesco ideale va da 60° a 80° così in questo caso, dopo un piccolo calcolo sul bilanciamento dei volumi e sullo spazio disponibile ho deciso di optare per 74° esatti. Gli stampisti tendono sempre a ridurre inizialmente le dimensioni consigliate quindi quando dimensiono un direttore di energia e la sua regione di giunzione mi tengo fin dall’inizio un certo margine progettuale correlato con il tipo di polimero utilizzato.
Il Datasheet del PMMA è sempre una parte ricca di utili informazioni a questo riguardo ed è estremamente importante considerare sia il Melting point che il Vicat quando si parla di giunzioni da ultrasuoni. Il PMMA è il vero re indiscusso della fanaleria automotive. È un materiale duro e rigido (ideale per le vibrazioni meccaniche degli ultrasuoni quindi), ha un’ottima resistenza alla trazione-compressione ed è trasparente alla luce filtrandone solo l’8%.
Questo è il primo progetto con l’azienda di Davide in cui saldiamo il fanale direttamente col sonotrodo sulla lente. Due anni fa abbiamo sviluppato insieme la saldatura di un fanale retronebbia e tutto è andato bene fin da subito, questo è il motivo per cui siamo qui oggi a condividere questo progetto così strategico.
Il retronebbia aveva una saldatura di tipo standard direttamente sul corpo così l’estetica era affidata alla speciale resina estetica che adesso negli ultimi posaggi è stata sostituita col GeroTech (per scoprire i vantaggi di questa nuova resina antigraffio leggi pure l’articolo dedicato).
Le dimensioni del retronebbia erano di poco superiori a 310 millimetri quindi una saldatura non ha presentato particolari criticità. Abbiamo trovato il setup corretto dopo poco più di un’ora e tutto è andato bene fin dalle prime saldature.
Qui sembrava tutta un’altra storia.
Saldatura estetica estrema. 12 chilogrammi e 450 millimetri di pura lega di titanio da far vibrare in modo possente e rapido, massimo 3 decimi di secondo per fondere il direttore di energia di almeno 7 decimi.
Decisamente una bella sfida!
Prima ancora di iniziare la saldatura è fondamentale controllare con una sezione al microscopio se il direttore di energia e tutta la regione di giunzione sono state realizzate rispettando le dimensioni del modello matematico. Questo è uno dei controlli fondamentali che differenzia un’azienda di ultrasuoni scarsa o mediocre da un’azienda strutturata e professionale. Il costo del microscopio elettronico rappresenta solo la prima barriera (un modello valido costa almeno 30.000 €). In realtà un’azienda seria sa che, oltre agli strumenti performanti, deve avere un team di persone con elevate competenze in tutti gli ambiti del processo. Persone che sappiano capire in modo rapido dove sono i problemi e come risolversi.
Chiaramente in Italia le aziende di ultrasuoni locali hanno al massimo 15-20 dipendenti, ognuno ha diversi compiti da svolgere e quindi troverai che la stessa persona fa il programmatore, il montatore meccanico e prepara anche i pacchi da spedire.
Poi ci sono le sedi italiane delle multinazionali spesso locate vicino a Milano. In questo caso chi si occupa dei test non ha magari mai parlato con chi ha progettato e sviluppato le saldatrici. Ha una conoscenza molto superficiale del software di gestione e quini fa quello che può. Salda alcuni pezzi, cerca di smanettare coi classici parametri come l’ampiezza, il tempo di saldatura (la modalità più amata dagli italiani!!), e poi ti dice che è colpa dei tuoi pezzi e di chi li ha stampati oppure che il polimero utilizzato non è compatibile…eccetera…eccetera…eccetera….
Ma non sei stanco di queste risposte poco professionali?
Si, ti capisco, a volte verrebbe da tirar loro addosso qualche bel sonotrodo!!
La prima cosa che devi fare quando hai qualche problema di saldatura a ultrasuoni è verificare il direttore di energia sia come lo hai effettivamente studiato e che si fonda così come è stato pianificato.
Qui sotto hai un esempio di questo studio.
Considera che la mia analisi statistica su oltre 1.000 progetti a partire dal 2010 conferma un dato scioccante. Solo il 28 % dei particolari segue in modo fedele il modello 3D (considerando anche le tolleranze chiaramente). Se poi partiamo dalla prima prova stampo il dato scende sotto il 10%.
Cosa significa questo?
Stai molto attento a quello che stai saldando!!
-
2 volte su 3 le tue parti non sono completamente a specifica!
Quindi prima di iniziare a le prove di saldatura fai una scansione al microscopio delle sezioni, solo così potrai aiutare il tuo amico stampista/stampatore a produrre particolari ideali per essere saldati.
Non ti ho ancora parlato di tutto lo studio del design, quale modello scegliere e come calcolare il corretto bilanciamento dei volumi, ma questo sarà argomento di un altro articolo.
Con Davide, pur essendo alle prime prove stampo con un pezzo non propriamente a specifica la saldatura ci ha regalato subito segnali molto positivi e il risultato della giunzione saldata lo vedi qui sotto con l’aiuto dell’amico microscopio.
Il direttore di energia è ben fuso, ben compresso contro la parete. La linea di giunzione è appena visibile ma in questo caso stiamo saldando 2 materiali diversi quindi è un effetto alquanto normale.
La tenuta ermetica a 1,5 bar viene raggiunta facilmente.
Come se la passa l’estetica?
Dopo alcuni tentativi siamo riusciti ad ottenere un risultato impeccabile. Anche Matteo della qualità col suo occhio attento e i suoi guanti da orologiaio di Zurigo conferma per lui il pezzo è conforme.
Anche la funzionalità è stata mantenuta con successo e questo per Davide e Matteo significa tornare in azienda con la sicurezza e la confidenza che il processo è stabile, le caratteristiche richieste soddisfatte e il Dott. Luppi (grande capo dell’azienda) si appenderà un’altra medaglia nella giacca…e nessuno sarà torturato in sala mensa….
Lo so che hai un sacco di domande per me!?
Non ti ho ancora detto come abbiamo fatto il setup dei parametri di saldatura….
Ancora una volta l’esperienza insieme al fiuto ci ho partati nella strada giusta.
Se avessimo dovuto applicare la formula standard per il calcolo della forza di trigger del PMMA saremmo andati completamente fuori strada. Il dato teorico è dato da:
La cosa sorprendente è i migliori risultati li abbiamo ottenuti applicando solo 300 N per circa 2 secondi di stabilizzazione. Anche questa volta l’intuizione ha vinto sul dogmatismo delle regole dove, a detta dello zio Vito:” …negli ultrasuoni c’è solo una cosa certa, niente è certo!”.
Per ottenere poi un processo quanto più possibile rapido e robusto abbiamo innalzato la velocità di fusione fino a 4 mm/s con un’ampiezza di 24 micron (48 micron per i fanatici delle misure picco-picco anglosassoni).
Dopotutto un bello sforzo per il Servo Drive che insieme al ParalliCer® (Active Melting Drive) ci ha evitato ogni deflessione anche con un carico così elevato e in continua variazione.
Come atteso, il drop in force iniziale si è prolungato solo per circa 40 millisecondi. I rimanenti 270 millisecondi di saldatura sono filati via lisci con la profondità di saldatura che seguiva la medesima regolarità della forza che è aumentata fino a 1.885 N.
Eccoti come sempre il setup completo con la massima trasparenza. Se hai qualche domanda, beh..sai sempre dove trovarmi!
In bocca al lupo e buone saldature!
Francesco
Lascia un commento